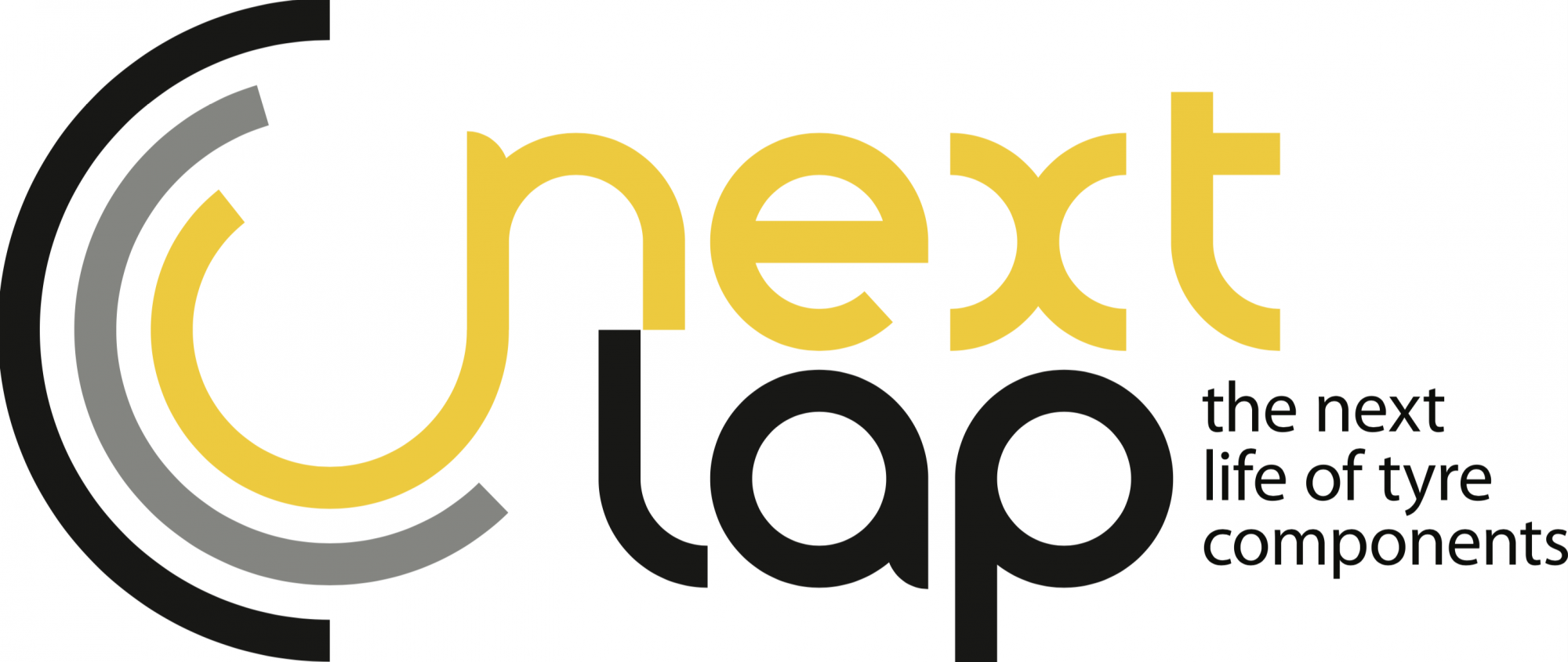
Empresas associadas à cadeia de valor do setor e um conjunto de empreendedores começaram a desenvolver em conjunto cinco projetos focados em dar uma segunda vida a materiais derivados da reciclagem de pneus em fim de vida e promover um mercado mais circular. Este foi o resultado do final do programa de inovação NextLap, promovido pela entidade gestora portuguesa Valorpneu e a recicladora multinacional de origem dinamarquesa Genan e gerido pela consultora de inovação colaborativa Beta-i.
O objetivo do programa, que teve a duração de nove meses, foi apresentar soluções, criadas em conjunto por empreendedores nacionais e internacionais e grandes empresas, a partir da reutilização dos componentes de pneus em fim de vida (granulado de borracha, fibras têxteis e aço).
Além da Valorpneu e da Genan, o programa contou com o envolvimento da Decathlon Portugal, das Infraestruturas de Portugal, das empresas de construção Grupo Opway e Pragosa, do Cluster Automóvel MOBINOV, da empresa de reciclagem Extruplás, da empresa de calçado Procalçado e da marca de sportswear Houdini.
A marca francesa de artigos desportivos Decathlon, ao lado dos parceiros de inovação Rubberlink e Tintex, é responsável por dois destes projetos-piloto, que consistem em protótipos de calçado fabricado com materiais de pneus descartados.
Os inovadores da portuguesa Rubberlink criaram uma solução de borracha de pneu desvulcanizada que permitiu à Decathlon Portugal produzir um protótipo de um sapato com uma sola de borracha 100% reciclada. Segundo dados da Genan, em comparação com o uso de matérias-primas virgens para produzir produtos semelhantes, para uma tonelada de pneu que é reciclado, são produzidas menos de 700kg de emissões de carbono.
Já os inovadores da portuguesa Tintex, através dos materiais fornecidos pela recicladora Genan, conseguiram reaproveitar o pó de borracha derivado do pneu para criar a gáspea de calçado de ginástica que será também testada pelo maior retalhista de produtos desportivos do país. Esta inovação permite usar o pó de borracha em algo que até agora não tinha sido equacionado. A Tintex foi ainda responsável pelo desenvolvimento de uma solução para aproveitar o têxtil derivado do pneu, que permitirá reutilizar um material que tem poucas aplicações económicas e, comparativamente a matérias-primas ‘standard’ feitas com couro, reduzir o consumo total de energia e água na sua produção. Possíveis aplicações para esta solução são, por exemplo, os selins das bicicletas.
Também a Infraestruturas de Portugal poderá vir a apoiar a implementação, em colaboração com os inovadores Pavnext e o parceiro Pragosa, de uma tecnologia para ser colocada nas estradas, coberta com borracha proveniente de pneus reciclados, que tem como objetivo desacelerar a velocidade dos veículos quando entram nas localidades. Juntamente com a Opway, a empresa pública tem ainda interesse em continuar a apoiar a Ruconbar na possibilidade de implementação de barreiras acústicas feitas de compostos de borracha derivada de pneu reciclado nas suas linhas ferroviárias, o que permitirá uma diminuição de 30% das emissões de carbono em relação produção de barreiras à base de óleo.
Para mais informações sobre o programa consultar o site do NextLap Program.
A Valorpneu foi falar com dois dos inovadores envolvidos neste programa – a Ruconbar e a Tintex – para conhecer os seus projetos e perceber as suas expectativas relativamente a este programa.
Barreiras acústicas com granulado de borracha
Ruconbar, Ivo Haladin
O que os levou a participar no programa de inovação NextLap?
Queríamos apresentar o nosso produto baseado no pneu em fim de vida a diferentes públicos e mercados e o NextLap parecia ser um local perfeito para isso.
Que projeto foi apresentado?
Ruconbar – Rubberised Concrete Noise Barriers. Ruconbar é uma barreira sonora de betão altamente absorvente e amiga do ambiente. A sua absorção incorpora 40% de grânulos de borracha reciclada de pneus usados de automóveis.
Onde pode esta solução ser implementada?
Em qualquer projeto de infraestruturas rodoviárias ou ferroviárias onde seja necessária proteção contra o ruído. Ruconbar é testado, certificado (CE) e pronto a ser implementado.
O programa correspondeu às vossas expectativas?
O programa cumpriu e excedeu as nossas expectativas. Conseguimos falar com produtores e clientes finais e planear uma aplicação piloto interessante.
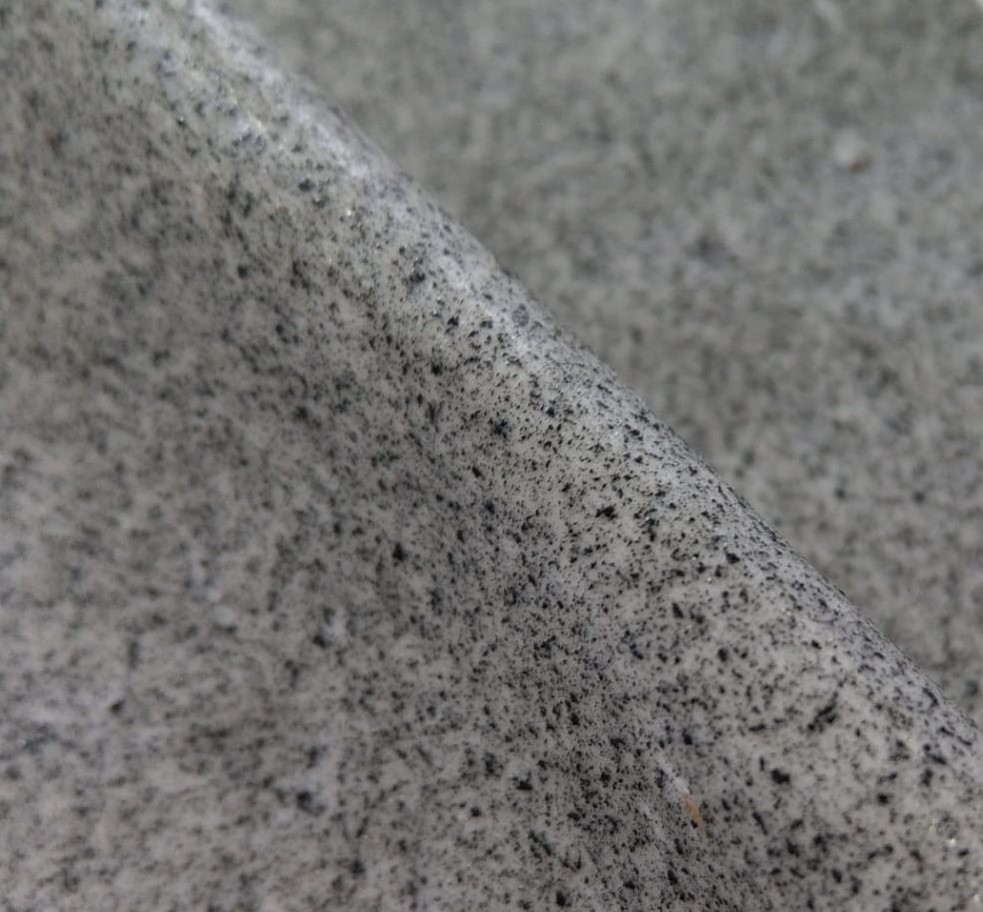
Tintex, Pedro Magalhães
Como foi utilizado o têxtil do pneu usado na produção de uma sapatilha?
No caso da Tintex, apesar do foco inicial poder ter sido fibras têxteis, os produtos finais foram desenvolvidos a partir de revestimentos de têxteis incorporando os resíduos de pneus em fim de vida. Neste contexto, foi possível, da nossa parte desenvolver dois revestimentos distintos, um em que incorporámos granulado de borracha e outro revestimento em que incorporámos um agregado de filamentos têxteis e fragmentos de borracha. A sabrina desenvolvida teve como base a utilização de têxtil revestido, com incorporação exclusiva de granulado de borracha, na sua parte superior.
Já tinham testado algo semelhante?
Os conceitos, de economia circular e de incorporação de resíduos, integram a génese nuclear da atividade de inovação da Tintex. Assim, neste contexto, a incorporação de resíduos e subprodutos de outras áreas é algo que vimos a trabalhar há algum tempo. No entanto, até a este desenvolvimento o foco tinha sido principalmente resíduos e sub-produtos de origem vegetal, sendo esta a primeira incursão neste tipo de produtos.
O programa NextLap correspondeu às vossas expectativas?
Sim, o programa Nextlap permitiu, e de acordo com as nossas expectativas iniciais, criar sinergias industriais relevantes que, felizmente, permitiram o desenvolvimento e a prototipagem de materiais, que promovem diferenciação à cadeia de valor de produtos do calçado pela incorporação de materiais provenientes de pneus em fim de vida.
Quais as principais dificuldades encontradas?
Existem sempre dificuldades técnicas, no entanto a capacitada equipa de inovação da Tintex tem conseguido competentemente ultrapassar os últimos desafios abraçados, sendo este um desses desafios. Outro desafio que ainda temos, neste momento, é o desenvolvimento de um material que respeite as especificações técnicas dos artesãos e consumidores, materializando os critérios do “esteticamente apelativo” e “robusto” naquilo que é a performance e durabilidade.
O que ainda está por fazer no âmbito deste projeto?
Neste momento, estamos a focar os nossos esforços no desenvolvimento específico dos materiais, tendo em conta as possíveis aplicações futuras – sapatilhas, mochilas, selins, casacos, entre outros. Após esta fase, avançaremos com a industrialização e, esperamos nós, também a comercialização dos produtos.